オンラインかじ
<ウェブサイト名>
<現在の時刻>
TOP ニュースリリースガイド ニュースリリースガイド一覧 新エネルギー 省エネルギー 材料 Focus NEDO FocusNEDO一覧 Focus NEDO第88号/特集 人とAIが協力し合う未来へ 次のAIが見えてきた Focus NEDO第87号/特集 省エネ・脱炭素への道をひらく 未利用熱エネルギー活用技術 Focus NEDO第86号/特集 AIエッジコンピューティング Focus NEDO第85号/特集 材料開発の革新に三位一体で挑む 超超プロジェクト 第84号/カーボンリサイクル・窒素循環・アンモニア発電・プラスチックリサイクル 資源循環社会への道 第83号/日本の主力エネルギーを目指す 再生可能エネルギー 第82号/イノベーション創出を加速 スタートアップ支援 第81号/実用化へのカウントダウン『セルロースナノファイバー』 第80号/イノベーションで未来をつくる NEDO40年のあゆみ 第79号/ムーンショット型研究開発事業-地球環境の再生へ Cool Earth & Clean Earth 第78号(技術戦略研究センター/スマートセル技術) 第77号(AI・ロボットのNEXTステージ/『オープンイノベーション白書』で読み解くイノベーション創出の今と未来) 実用化ドキュメント 実用化ドキュメント一覧 新エネルギー 省エネルギー 環境問題対策 電子・情報 材料 ロボット・AI・福祉機器 バイオ・医療 NEDO Channel NEDO Channel一覧 新エネルギー 環境問題対策 電子・情報 ロボット・AI・福祉機器 国際 分野横断 その他 NEDO Channel --> 検索 NEDO Channel NEDO公式X NEDO公式Facebook NEDOホームページ トップページ 実用化ドキュメント より微細な半導体デバイスを作るために、表面加工に欠かせないレーザー光源を開発 CONTENTS INTRODUCTION 表面加工の微細化 180nm → 32nm(原子約300個分) BEGINNING IT社会の進化を、根源から支える フォトリソグラフィ技術 BREAKTHROUGH プロジェクトの突破口 FOR THE FUTURE レーザー波長だけではない、 様々な微細化技術を研究開発し、世界トップへ FACE レーザー研究開発一筋、 微細化で情報通信革命の未来をこれからも担う なるほど基礎知識 メニュー閉じる 電子・情報 F2レーザリソ技術の開発 より微細な半導体デバイスを作るために、表面加工に欠かせないレーザー光源を開発 ギガフォトン株式会社 取材:December 2009 INTRODUCTION 概要 表面加工の微細化 180nm → 32nm(原子約300個分) (KrFソリグラフィ) → (ArF液浸ダブルパターニング ソリグラフィ)※nmはナノメートル、10-9メートル=10億分の1メートル 私たちの身の回りには、コンピューター(半導体集積回路)が内蔵された製品があふれています。生活をより便利にサポートしてくれるこれら家電やIT機器は、常に高性能化を求められています。コンピューターの高性能化は、心臓部のマイクロチップ(半導体集積回路)の微細化とほぼ同義です。微細化には、より細い配線を半導体内部に作る必要があり、そのためには超極細の溝を刻む、「フォトリソグラフィ」という技術が欠かせません。そして、フォトリソグラフィの技術の要となるのがレーザー光源です。フォトリソグラフィ用のレーザー光源の開発競争で勝ち残ったメーカーは、世界でたったの2社。その一つが、日本のギガフォトン社です。 BIGINNING 開発への道 IT社会の進化を、根源から支えるフォトリソグラフィ技術 めざましい処理能力の進歩を遂げるコンピューター。その処理能力の進歩に合わせて次々と提供されるIT分野の新サービスや3D映画を初めとするバーチャル映像。そうした流れを支えているのが、コンピューターの心臓部であるマイクロチップ(半導体集積回路)の微細化です。回路が微細になればなるほど、信号伝達の高速化や省エネ化、低価格化を図ることができます。 マイクロチップは、ウエハとよばれる円板状のシリコン半導体の上にパターン(配線)を作り込んで製造されます。つまり微細化のためには、より細かいパターンを作る加工技術が必要となります。半導体産業には集積密度が約18カ月で2倍になるという「ムーアの法則」※1があり、微細加工もその法則に従って日々進歩してきました。 現在、微細加工技術の主役は「フォトリソグラフィ」です。これは、シリコン・ウエハにレーザー光を当てて溝を作る技術です。ウエハの表面に感光性の物質「フォトレジスト」を塗り、パターン状に穴が空いた「フォトマスク」を被せます。そこにレーザーを当て(露光)レジストを感光させ現像すると、露光した部分は削られて露光しない部分は残り(レジストの性質によりまたは逆)、パターンが形成されます(なるほど基礎知識参照)。 回路を作り込むシリコン・ウエハ ギガフォトンの最新型レーザー光源発生装置 フォトリソグラフィによる微細化では、露光光源であるレーザーの波長を短くする必要があります。レーザーは光であるため、原理的には波長に相当する幅の溝しか作れません。微細加工するためには、レーザー波長をとにかく短くする必要があるのです。 数十nm(ナノメートル:ナノは10億分の1)の"溝"を作る微細加工を目指して、多くのメーカーがレーザー光源の開発にしのぎを削ってきました。その結果、レーザー光源開発のトップ企業となったのが、ギガフォトン株式会社です。 波長248nmのKrFエキシマレーザー※2を使用した場合、他の加工技術と組み合わせて180〜90nmの"溝"まで作ることができました。ギガフォトンではこれを、波長193nmのArFエキシマレーザーを利用して、90〜32nmまで微細加工できる技術を開発しました。"溝"幅が、原子数百個分という超極細加工技術です。 ※1 ムーアの法則集積回路におけるトランジスタの密度が18~24カ月ごとに倍になるという経験則。集積密度はコンピューターの演算速度に直結する。そのため、演算速度が18~24カ月ごとに倍になるとも表現される。 ※2 エキシマレーザー希ガスやハロゲンの混合ガスを用いてレーザー光を発振させる装置。希ガスとしてはアルゴン(Ar)、クリプトン(Kr)が、ハロゲンとしてフッ素(F)などが使われる。図2、3参照。 半導体産業の主導権を巡って勃発した、日米レーザー技術開発競争 ギガフォトンは、レーザー光源開発のために2000年8月に設立された、株式会社小松製作所とウシオ電機株式会社との合弁会社です。小松製作所出身であるギガフォトン取締役専務執行役員の溝口 計さんは、「小松製作所では、1980年ころからKrFレーザー(248nm)の研究開発を始めました。ただ、当初はリソグラフィとは関係ないものでした。しかし、1980年代中頃から、世界中の大学・企業の研究者などが、KrFレーザーはフォトリソグラフィに使えるのではないか、と指摘し始めて、一気に研究開発が進みました」と振り返ります。 ギガフォトンの生産ライン。仕切り間に置かれた箱状の機械が、レーザー光源発生装置 1990年代後半に入ると、光源開発の最先端はKrFレーザーから波長193nmのArFレーザーに移っていました。ここで、半導体産業で遅れをとったアメリカが半導体産業で次の主導権を握るため、さらに波長の短いF2レーザー(157nm)の開発を目標に掲げ、産・学・国立研究所の協力で積極的に開発をすすめました。それに対抗する形で、日本でも小松製作所などが1998年からF2レーザー開発をスタートさせました。 さらに2000年4月からNEDO「F2レーザリソ技術の開発プロジェクト」(2002年度まで)が始まり、レーザー光源メーカーの小松製作所とウシオ電機、ステッパー(縮小投影型露光装置)メーカーの株式会社ニコン、キヤノン株式会社、東京大学、九州大学、および主要半導体メーカがF2レーザーの開発に加わりました。ついで2000年8月にはギガフォトン社が設立されました。 日本ならではの発想力で主導権を死守、新技術でArFレーザーが主役に返り咲き ところが、その矢先の2001年、ニコンが独自にF2レーザーを超える新技術を開発した、と発表しました。その新技術は、「ArF液浸技術」で、屈折率という光の性質を利用したものでした。 光は真空中を光速で移動しますが、ガラスや水を通過するときには速度が落ちます。速度は単位時間(秒)あたりの距離(メートル)ですから、それが落ちるということは時間あたりの距離が縮まる、つまり波長(ナノ・メートル)が短くなることを意味します。 ニコンは、加工するシリコンウエハを、純水の中に沈め(液浸)、そこにArFレーザーをあてることで(図3)、134nm相当のリソグラフィ性能が出せるようにしたのです。 これを知ったギガフォトンでは、F2レーザー開発を一旦断念※3し、液浸用ArFレーザーに注力することにしました。「ただ、F2の開発は無駄ではなかった」と溝口さんは言います。液浸では厳しい解像力が要求され、レジスト感度が下がるなどの課題があり、それを克服するために液浸用ArFレーザーにも高出力化、高いスペクトル純度などを要求され、技術的により困難なF2レーザー開発で得た様々な先端技術が役に立ちました。すなわち、2003年度のNEDOプロジェクトで達成した高出力化、短波長化に欠かせないインジェクションロック方式(ブレークスルー参照)などです。おかげで高性能ArF液浸リソグラフィ用のレーザーを開発することができ、後のシェア向上の下地となりました。 図3 液浸技術の模式図シリコン・ウエハを媒質(純水、屈折率n=1.44)に沈めたところにレーザー光を当てる。 インジェクションロック方式について説明する溝口専務 ※3 F2レーザー開発F2レーザー開発は、技術的には東京大学物性研究所の渡部俊太郎教授、九州大学大学院システム情報科学研究院の岡田龍雄教授の協力で成功している。波長幅0.2pm、発振周波数4kHz、出力20Wを達成。これは波長157nmの領域のレーザーでは世界初の快挙である。 BREAKTHROUGH プロジェクトの突破口 レーザー波長が短いほど微細加工に有利なのですが、もう一つ重要な性質として波長幅があります。仮に10nmの光源があったとしても、実際には8nmから12nmに広がった光であれば、誤差が大きすぎてきれいに加工できません。波長の幅をいかに狭くするかがポイントなのです。 ギガフォトンでは、レーザーの波長幅を狭くするため光源に特殊な分光器を使っています。光源から出た光を分けて、必要なものだけ取り出して使うのです。ところが、プリズム、回折格子、ミラーなどの分光素子はCaF2などの材料を使った特注品で、これはレーザー出力が20W以上になると劣化してしまいます。エキシマレーザーの高出力化は工程時間の短縮につながるため重要な性質で、分光器によって出力の上限が決められてしまうのは大きな問題です。 そこで、分光器を使いつつ高出力のレーザーを発振できるよう、インジェクションロック方式を採用することにしました。インジェクションは注入、ロックは波長と位相※4の固定という意味で、赤外や可視では一般的ですが、深紫外領域のレーザー装置では世界初の試みでした。この方式は、第1段のレーザーで約1Wという低出力ですが波長の幅が狭いレーザーを作り、それを第2段のレーザーで増幅させて高出力化するものです(図4)。インジェクションロックの開発に成功した結果、193nmのArFレーザーにおいて、実測で0.25pm(ピコメートル:ピコは1兆分の1)という狭い波長幅を達成することができました。 ※4 位相波の中のどの位置にあるかをいう レーザー光源発生装置に使用される分光器 図4 インジェクションロック方式 第1段階では、左下の分光器で波長ごとに分けて、必要な波長幅の光を中央のレーザーに戻す。第2段階では、それを増幅して高出力レーザーにする。 FOR THE FUTURE 開発のいま、そして未来 レーザー波長だけではない、様々な微細化技術を研究開発し、世界トップへ 波長の短いレーザー光源を開発するのは、容易なことではありません。そこでステッパーメーカーは、液浸のように露光工程での技術を向上させることで、レーザー波長を変えずに、実効的に細い溝を作る方針をとりました。そこで開発された新しい技術が、ダブルパターニングとレジストのk1ファクターという微細化特性値の最小化です。ギガフォトンは後者の改善に貢献しました。 ダブルパターニングとは、露光を2回行う方法です。1回目の露光で波長相当のパターンを作ったあと、ウエハを半波長分ずらして再び露光します。原理的には波長の1/2に相当するパターンが描けるのですが、実際には位置決めが非常にシビアなため、実現は相当難しいものでした。 図5 ギガフォトン社製品のラインナップムーアの法則をもとにしたロードマップに即したスピードで、レーザー光源開発を続けている。 k1ファクターとはレーザー光がウエハに当たり、波長の何分の1までの像が作れるかを示す値です。縮小投影レンズの性質とレーザー光の波長分布により決まる焦点面での光の分布特性と、レジストの感度特性から決まります。これをたとえば0.5にできれば、波長の1/2に相当するパターンが描けます。ギガフォトンはレーザーのスペクトル分布を精密に制御することで、焦点面での光の分布を安定化し、低いk1ファクターのプロセスを実用化することに貢献しました。 ArF液浸リソグラフィでは134nm相当の分解能があるので、この2つの技術を組み合わせると、理論上は波長の1/4に相当するパターンが仕上がり、32nm相当の解像力になります。ほかにも、インジェクションロック方式の開発(ブレークスルー参照)など、あらゆる技術向上をはかりました。その結果、レーザー光源開発のトップを走ることができているのです(図5)。 ここまで到達するには相当な開発費がかかりましたが、「この研究を続けられたのはNEDOプロジェクトのおかげです。これがきっかけになって、あまり開発費を気にせず積極的に技術開発に取り組むことができました。NEDOプロジェクトの支援がなければ、わが社のArFレーザーは世に出ていなかったと思います」と、溝口専務は口にします。 NEDOプロジェクトで培った半導体関連企業間の研究連携が販路維持に貢献 ArFレーザー光源メーカーは、現在、世界で米サイマー(Cymer)社とギガフォトン社しかありません。1990年代から国内外で多くのメーカーが開発に乗り出しましたが、競争の末に生き残ったのがこの2社なのです。ギガフォトンのArFエキシマレーザー光源の世界シェアは、2003年以前は10%程度でしたが、その後、着実にシェアを伸ばし、2008年に50%に到達し、2010年には約60%を見込んでいます。地域的なことから、サイマーは欧米に強く、ギガフォトンはアジアに強い特徴があります。納入先はニコン、キヤノンなどのステッパーメーカーで、設立してからの通算販売台数は約700台です。 製品開発も売り上げも順調にきている理由を、溝口専務は「NEDOプロの垂直統合的なところが良かった」と言います。「F2レーザーリソ技術の開発」には、光源メーカーだけでなくステッパーメーカーが入っていました。さらに、プロジェクトの中には総合調査研究というテーマもあり、それにはステッパーのユーザーである国内主要半導体メーカーも関わっていました。ギガフォトン執行役員経営企画室長の佐藤日出一さんが、「ニーズからシーズまですべて含まれていた」というように、川上から川下までのユーザーの声を開発に反映できる体制をNEDOが考えて構築したことが大きかったと考えています。 佐藤経営企画室長 製品の最終チェックを行う、生産技術者 また佐藤室長は、自社製品がレーザー光源の世界標準となっている現状に「"色"がないのが良い結果を生んだ」と言います。「光源、ステッパー、半導体の各企業が組んで独自仕様の製品を出すことも可能だったと思います。しかし、ギガフォトンはステッパーメーカーのどことも組まなかったため、どのメーカーにも適合する製品を作り上げることができました」 マイクロチップ微細化の物理的限界に迫る ギガフォトンという社名は、光子を意味するフォトンの上に、コンピューターが近い将来(設立の2000年から見て)到達するビット数や半導体産業で一般的に必要とされる精度109などを意味するギガを冠したものです。しかし2010年に入った現在、新たな、そしておそらく究極の目標が見えてきました。 マイクロチップなどの半導体デバイスの微細化は、理論的に原子数十個に相当する数nmまでが可能であると考えられています。この最終目標に到達できるとされるのが、13.5nmのEUV(極端紫外線)光源を使ったEUVリソグラフィです(図5参照)。 液浸やダブルパターニングを組み合わせれば、原理上は波長3.4nm相当のパターニングが可能です。ムーアの法則をもとにしたロードマップによれば、2013年までにEUV光源を開発する必要があります。すでにウシオ電機、コマツ、ギガフォトンが参加するNEDOプロジェクトにて研究開発が進んでいます。溝口専務は「開発費がArFの何倍もかかりそうだ」と言いますが、その開発費に見合う性能を持ったEUV光源を開発してくれるに違いありません。(2009年12月取材) 中央の円形部分から微細加工用のレーザーが発振される 光源発生装置の制御盤 開発者の横顔 レーザー研究開発一筋、微細化で情報通信革命の未来をこれからも担う 溝口専務は小松製作所に入社後、約30年もの間、レーザーの研究開発に携わってきました。「ずっとレーザーに関わってこられたのは、技術者としては幸せだったと思います」 KrF,ArF,F2レーザー開発の中心的役割を担ってきた溝口専務ですが、当初たくさんあった競合他社が、いま世界で2社しかいなくなった状況を振り返り、「開発を始めたときは、最後まで生き残れるとは思わなかった」と言います。しかし、開発を完了させた現在の心境を「達成感よりも、まだまだこれからという気持ち」と語ります。それは次に究極の難関、EUV光源が控えているからです。「ArFで終わりだと思っていたんですがねえ…。でもEUVを実用化するまでは、まだまだ走るのをやめられません」 ギガフォトン株式会社溝口専務 なるほど基礎知識 マイクロチップが、CPU、携帯電話部品、フラッシュメモリーなどの最終製品に至るまでには、多くの工程を必要とします。 (1) ウエハ製造 マイクロチップの母材となるウエハの原料には、主にシリコン半導体が用いられます。シリコンは単結晶であることが求められ、不純物の少なさ、結晶の欠陥の少なさ、大きさが重要となります。 (2) 表面処理1:ドーピング ウエハにドープ物質を打ち込んで不純物濃度をコントロールし、半導体として機能させます。 (3) 表面処理2:フォトリソグラフィ 感光性の物質「フォトレジスト」を塗り、パターン状に穴が空いた「フォトマスク」にレーザーを当て、その光をレンズで転写して露光しパターンを形成します。 図1 マイクロチップの製造工程 図2 進歩するフォトリソグラフィ (4) 表面処理3:ゲート、配線の作成 絶縁膜を生成してゲート(端子)を作り、金属スパッタリング※5によって配線を作ります。(続けてシリコンの堆積、(2)、(3)の作業を繰り返し行い、多層のマイクロチップを作ることも可能です) ※5 スパッタリング加速されたイオンを材料物質に衝突させ、空間内に放出された材料で、基板上で薄膜を形成させる薄膜製造技術 (5) 完成品へ 製造されたウエハを、レーザーや砥石を用いてチップの形に切り離して、チップ上の端子とパッケージの端子を、細い金属(金やアルミ)線で接続させます。さらに、衝撃や水分などから守るため、熱硬化性樹脂で固めます。これで完成。フォトリソグラフィが考案された当初は、ウエハ表面にマスクを密着させてレーザーを当てる等倍露光が行われました。しかし、微細化が進むにつれてマスクを精度良く作ることが困難になってきたため、マスクは大きいままで、集光レンズを使ってウエハ上にイメージを縮小転写する縮小投影露光に変わりました。 お読みいただきありがとうございました。ぜひともアンケートにお答えいただき、お読みいただいた感想をお聞かせください。いただいた感想は、今後の連載の参考とさせていただきます。 アンケートに回答する (法人番号 2020005008480) NEDO WebMagazineとは サイト利用について ©New Energy and Industrial Technology Development Organization. All rights reserved. Top -->
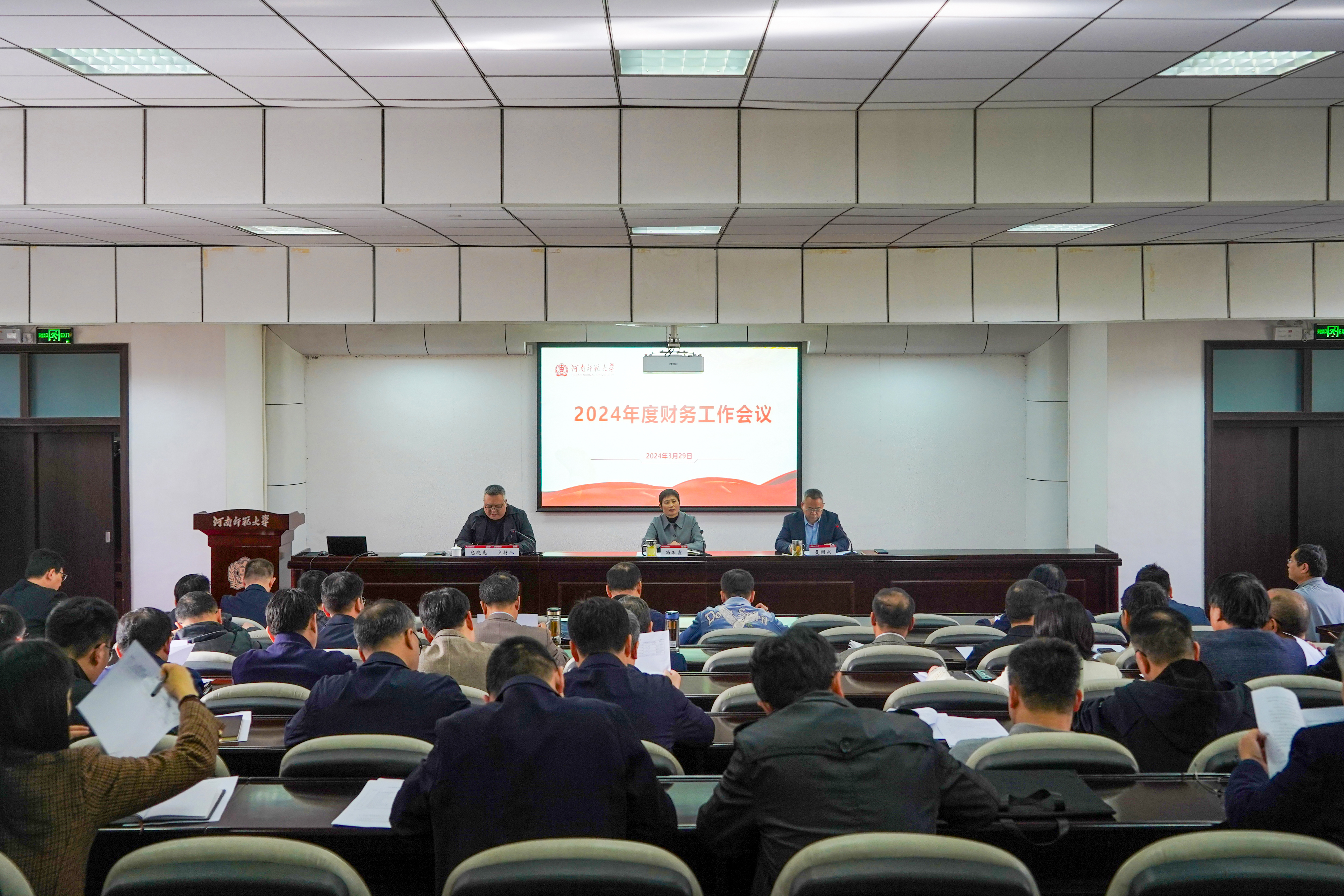