サルフォード・シティfc
<ウェブサイト名>
<現在の時刻>
TOP ニュースリリースガイド ニュースリリースガイド一覧 新エネルギー 省エネルギー 材料 Focus NEDO FocusNEDO一覧 Focus NEDO第88号/特集 人とAIが協力し合う未来へ 次のAIが見えてきた Focus NEDO第87号/特集 省エネ・脱炭素への道をひらく 未利用熱エネルギー活用技術 Focus NEDO第86号/特集 AIエッジコンピューティング Focus NEDO第85号/特集 材料開発の革新に三位一体で挑む 超超プロジェクト 第84号/カーボンリサイクル・窒素循環・アンモニア発電・プラスチックリサイクル 資源循環社会への道 第83号/日本の主力エネルギーを目指す 再生可能エネルギー 第82号/イノベーション創出を加速 スタートアップ支援 第81号/実用化へのカウントダウン『セルロースナノファイバー』 第80号/イノベーションで未来をつくる NEDO40年のあゆみ 第79号/ムーンショット型研究開発事業-地球環境の再生へ Cool Earth & Clean Earth 第78号(技術戦略研究センター/スマートセル技術) 第77号(AI・ロボットのNEXTステージ/『オープンイノベーション白書』で読み解くイノベーション創出の今と未来) 実用化ドキュメント 実用化ドキュメント一覧 新エネルギー 省エネルギー 環境問題対策 電子・情報 材料 ロボット・AI・福祉機器 バイオ・医療 NEDO Channel NEDO Channel一覧 新エネルギー 環境問題対策 電子・情報 ロボット・AI・福祉機器 国際 分野横断 その他 NEDO Channel --> 検索 NEDO Channel NEDO公式X NEDO公式Facebook NEDOホームページ トップページ 実用化ドキュメント 世界で圧倒的なシェアを誇る、電子ビームマスク描画装置 CONTENTS INTRODUCTION 年間売上数億円から400億円の事業へ BEGINNING 超微細回路を大量生産するための フォトマスク BREAKTHROUGH プロジェクトの突破口 FOR THE FUTURE 新技術の研究開発継続で精度を向上 FACE 社内初の商用化を目指し チームが一丸となった なるほど基礎知識 NEDOの役割 メニュー閉じる 電子・情報 超先端電子技術開発促進事業 世界で圧倒的なシェアを誇る、電子ビームマスク描画装置 株式会社ニューフレアテクノロジー 取材:November 2012 INTRODUCTION 概要 年間売上数億円から400億円の事業へ スマートフォンやタブレットPCなどデジタル情報通信機器の普及により、わたしたちの生活環境は大きく変化しようとしています。そして、このような高機能かつ、小型・軽量な情報通信機器を支えているのが、かつてないほど高密度化、微細化が進んだ半導体集積回路(LSI)です。回路の太さはすでに、nm(ナノメートル=10億分の1m)の領域に入っています。そうした超微細な回路の大量生産を可能にするのが、半導体集積回路の「ネガフィルム」にあたる「フォトマスク」です。1990年代半ばまでは、フォトマスクの製造装置は米国メーカーが主流でしたが、NEDOでは将来のLSI高密度化、微細化に備えて、1995~2001年に、「超先端電子技術開発促進事業」プロジェクトを実施、より微細な回路を描画できる「電子ビームマスク描画装置」の研究開発を進めました。プロジェクトに参加した株式会社ニューフレアテクノロジー(当時、株式会社東芝、東芝機械株式会社)では、1998年に180nm設計寸法LSI対応の電子ビームマスク描画装置開発に成功したのを皮切りに、最新機種では22nmまでの超微細加工が可能になり、現在では90%以上の世界シェアを獲得するに至っています。 BIGINNING 開発への道 超微細回路を大量生産するためのフォトマスク LSIを高性能化するには回路の集積密度を上げる必要があります。そのためには、同じ大きさのチップに、より細かい回路を描き込む技術が求められます。シリコンウエハに直接回路を描く方法(直接描画)もありますが、「フォトマスク」と呼ばれる回路パターン原版を用いる、「ステッパー露光」が量産LSIの製造方法です。 フォトマスクには、微細な回路パターンが刻まれており、それをステッパーと呼ばれる装置でシリコンウエハ上に露光・転写することによって、LSIの大量生産を可能にしています。フォトマスクは、厚さ約6mmガラス板の上に厚さ0.1μm(μは100万分の1m)程度の金属(クロム)の薄膜を成膜したものです。転写では、フォトマスクを介して、上から光を照射すると、金属薄膜が除去されたところだけを光が通過し、レジスト(感光剤)を塗ったシリコンウエハ上に回路パターンが縮小転写される仕組みになっています。 フォトマスクを写真のネガフィルム、半導体ウエハを印画紙と考えると分かりやすいでしょう。フォトマスクに刻む回路パターンは、シリコンウエハ上に転写する回路パターンの約4倍に拡大したもので、1つのLSIを作るには、数十枚の異なる回路パターンが刻まれたフォトマスクが使われます。「電子ビームマスク描画装置」は、このフォトマスクを製造する装置です。 フォトマスク(写真は装置の位置調整用のマスク) 図1 フォトマスク作成の原理 マスク露光の限界を超えるための電子ビーム描画装置開発 集積回路の大量生産を可能にする「フォトマスク」ですが、半導体の集積化が急速に進んでいた1980年代ごろには、光転写による微細加工はやがて不可能になるのではないかとも危惧されていました。LSIパターン露光の際に、LSIに刻まれる回路パターンの線幅の最小寸法を下げるためには、回路パターンの線幅 より短い波長の光が望まれるためであるためでした。 その解決方法として期待されたのが電子ビームによる直接描画です。この電子ビームの波長は、加速電圧10kVで0.012nmと光に比べて4桁以上小さく、線幅が1μm以下になっても問題がありません。 ただしそのためには、電子を加速して固体に衝突させたときに起こる電子の散乱現象である「近接効果」を克服しなければなりませんでした。株式会社東芝と東芝機械株式会社(分社化により、現・株式会社ニューフレアテクノロジー)では、1970年代から電子ビームによる「直接描画」及び「マスク描画」技術の開発を開始、1984年から「マスク描画」と「直接描画」に向けた近接効果補正に関する研究開発に着手し、1995年には一定の成果を上げるまでになっていました。(「近接効果」については、「ブレークスルー」を参照) 直接描画から電子ビームでのマスク製作へ しかし一方で、直接描画で従来のような生産速度でLSIを大量生産することは難しいことでもありました。より微細な回路パターンの高精細なマスクを製作することができれば、露光・転写に光を使っても高細密なLSIを製造できます。ただし、加速度の低い電子ビームや光(レーザー等)を利用していた当時のマスク描画装置では、その当時の次の世代のLSIで要求される精度と描画速度を実現することが困難になりつつありました。 そうした中、世界に先駆けて、電子ビームによる細密なマスク描画装置を開発・実用化した企業(イーテック・システムズ社)が米国に出現しました。同社は一時90%以上のシェアを占めるまでになり、高価格戦略を維持することもできました。このプロジェクト開始当時は、イーテック社のマスク描画装置が最先端でしたが、次の世代の微細なマスク描画はまだ開発途上でした。 状況打破のために、日本でも早急にコストパフォーマンスに優れ、高精度で短時間に高精細なマスクパターンを描画する、その次の世代の電子ビームマスク描画装置を開発する必要がありました。そこで、NEDOでは1995年より「超先端電子技術開発促進事業」プロジェクトを実施したのです。 東芝と東芝機械は、過去のマスク描画と直接描画で培った近接効果補正技術を活かして同プロジェクトに参加し、電子ビームマスク描画装置の研究開発に取り組みました。近接効果補正の研究開発は、社内向けに基礎研究から始められたものでしたが、NEDOプロジェクトを通して実用化に向けた研究段階に進み、その成果を基に商用化を目指すことにしました。 両社は3年間の研究開発の結果、電子ビームマスク描画装置「EBM-3000(LSI設計寸法180nm)」の開発に成功。1998年に東芝機械から同社製の次世代の高精度高速マスク描画装置が商用機として販売開始されました。2002年には東芝機械から半導体装置事業部が分社・独立して、株式会社ニューフレアテクノロジーが創設されました。同社では現在もNEDOプロジェクトで開発された技術を基に装置のバージョンアップを続けています。最新機種の「EBM-8000(LSI設計寸法22nm)」は「EBM-3000」から数えて7代目の描画装置に当たります。 従来の数十分の1の細かさで回路パターンが描画できる「可変成形ビーム」 ニューフレアテクノロジーが開発した電子ビームマスク描画装置「EBMシリーズ」には、他社の装置と比べて多くの特長がありますが、その代表例を挙げると、「可変成形ビーム」「ステージの連続移動」「50kVの高加速電子ビームによる描画」の3点があります。 1点目の「可変成形ビーム」とは、四角形と三角形の図形を使って回路パターンを成形する方法です。電子ビームが2種類の成形アパーチャを通って、フォトマスクに照射されます。アパーチャとは開口、窓、穴といった意味です。2番目の成形アパーチャには、鍵穴のような形の穴が空いていて、電子ビームをその穴の縁を通過させて成形します(図2)。 図2 可変成形ビームの仕組み。最大の特色が鍵穴状の第2成形アパーチャ。マスクに正方形と二等辺三角形のどちらかの形を照射、その組み合わせで複雑で微細な回路を描くことができる 2種類の成形アパーチャの間には、周囲8方向から中心に向けて設置された成形偏向器が設置されています。この成形偏向器に電圧を印加することで、電子銃から放たれた電子ビームを曲げたい方向に曲げることができ、第2成形アパーチャの狙った位置に第1成形アパーチャ像の電子ビームを照射することができます(図3)。 その下には、成形された電子ビームをマスク上の希望の位置に照射する位置決めのため、同様の構造の偏向器が搭載されています(図3)。 図3 電子線マスク描画装置の仕組み 当時、主に使われていた他社の装置ではインクジェットプリンターのようにドット描画方式が主流でした。しかし、ドット描画方式には、回路が複雑でも単純でも、描画面積が同じであれば同じだけ時間がかかること、また、ドットの大きさよりも細かい線幅を描画することができないことなどの短所がありました。一方、可変成形ビームであれば描画に要する時間は回路パターンの複雑さに応じて変化するため、ドットで描画するよりも高速で、より細かい線を描画できます。 ニューフレアテクノロジーの吉川良一顧問は、「たとえば、ドット直径が100nmとすると、ドット描画方式の場合、100nm単位でしか線幅を調整できません。それに対し、可変成形ビームだと、初期のEBM-3000型の場合でも1.25nm単位で調整が可能です。ドット描画方式に比べて数十分の1の細かさで回路パターンの描画が可能です」と説明します。 また、描画装置統括部兼検査装置技術部の玉虫秀一技師長はこう話します。「1995年当時、電子ビームマスク描画装置で圧倒的なシェアを誇っていた米国のイーテック・システムズ社はドット方式を採用していました。ドット描画方式に代わる微細な描画技術を実用化できなかったことが、その後の同社の市場撤退につながったとも言われています」 編向器やアパーチャが収められている鏡筒 マスクを連続的に動かしなから高速に回路パターンを描画 2点目の「ステージの連続移動」とは、マスクが乗っているステージを動かしながら電子ビームを照射するという方法です。 装置の電子ビームを当てることができる面積は意外と狭く、1995年当時で1mm四方、現在の最新モデルでは200μm四方しかありません。そのため、回路パターンを描画するには、電子ビームではなくマスク自体を動かす必要があります。 ステージの動かし方には2通りあります。一つ目はステージを最適な位置に移動、一旦停止して描画、終わったらまたステージを次の最適位置に移動するという方法です。二つ目は停止することなく、絶えずステージを動かし続けて描画する方法です。当然のことながら、ステージを停止させるよりも高速に処理できます。しかし、それだけ高度な位置決め技術が要求されます。 描画装置技術部の服部芳明さんはこう説明します。「ステージを連続移動させる際に最も重要な点は、マスクの現在の位置を正確に把握すること。そこで、当社では、『ステージレーザーインターフェロメーター』と呼ばれる装置でマスクの位置を計測し、さらに、計測からビーム照射までの時間の遅れを予測し、位置を修正するトラッキング技術を実装した装置を開発しました。その結果、ステージの高精度な移動制御を実現しました」 精度向上に大きく影響した高加速電子ビーム 3点目の「50kVの高加速電子ビームによる描画」とは、電子ビームを高加速電圧で照射しながら描画する方法です。高加速電圧で照射するメリットは、高い解像度で描画をできることにありますが、加速電圧を上げると、厄介な現象が顕著に起こります。それが「近接効果」です。それを避けるため、1995年当時は主に10~20kVの電子ビームが主流でした。 マーケティンググループ参事の阿部隆幸さんは、「EBMシリーズの2点目までの特長は東芝と東芝機械がNEDOプロジェクト以前から開発してきたものです。近接効果の補正技術をブラッシュアップし、10~20kVではなく、50kVという高加速電圧の電子ビームを用いた高速・高精度のマスク描画装置を実用化できたことが、本プロジェクト最大の成果と言えるでしょう。さらに、現在、弊社が世界シェア90%を達成できた主な要因にもなっていると思います」と語ります。 高加速電子ビームの偏向アンプ 図4 電子ビームマスク描画装置の装置構成図。「電子光学鏡筒」に図3の装置が組み込まれている BREAKTHROUGH プロジェクトの突破口 LSIの微細化、高集積化が進む中、フォトマスクの回路パターンを光ではなく電子ビームで描画する「電子ビームマスク描画装置」の研究開発を進める東芝と東芝機械(分社化により、現・ニューフレアテクノロジー)では、「近接効果補正」という大きな難問をクリアする必要がありました。両社では1984年から取り組んできた「直接描画」方式の研究成果を応用、進歩させることでこの壁を乗り越えました。 正確な回路が描けなくなる電子の散乱、反射現象 「近接効果」とは、照射した電子ビームがマスクのガラスなどで散乱、反射して、設計通りの線幅の回路パターンが転写出来なくなってしまう現象です。 例えば、10kVという弱い加速電圧で電子ビームをマスクに照射すると、表面に塗布されたレジスト内では「前方散乱」という現象が顕著に起きて、回路パターンがぼやけてしまいます。前方散乱とは電子ビームがレジスト内の原子によって散乱され、進む方向と同じ前方、もしくは横に広がる現象のことです。 一方、約20kV以上に電子ビームの加速電圧を高めると、電子ビームは高速でレジストを通り抜けます。通過時間が短くなるため、前方散乱の広がりは小さくなります。ところが今度は、突き抜けた電子ビームがレジストの下にあるガラス層で反射、散乱し、再度レジストを露光してしまう現象が顕著になります。こちらは、電子ビームの進行方向と逆の方向に散乱するので、「後方散乱」と呼ばれています(図5)。 図5 近接効果とは? 高い寸法精度でマスクを描画するにはシャープなパターン形成のできる電子ビームが要求され、そのためには少なくとも50kVの加速電圧が必要です。しかし、50kVで照射すると、後方散乱によって影響を受けるレジストの範囲は周囲約30μmにも及んでしまいます。回路パターンが密である箇所では、それだけ多くの後方散乱を受けることになり、線幅が太くなってしまいます。近接する部分が影響するので、近接効果と呼ばれているのです。 つまり、加速電圧を下げれば前方散乱の影響でパターンがぼやけてしまい、加速電圧を上げれば後方散乱により線が太って、いずれにせよ設計通りのパターンが描画できないという現象が起きてしまうのです。この変動による寸法変動は最大で約200nmに及び、当初目標としたLSI設計寸法180nm(マスク上で720nm)のマスク製造には許容できない大きさでした。 電気回路制御で近接効果を補正し設計通りの回路パターンを実現 このような中、近接効果の補正技術を担当した阿部さんは、回路パターンが密なところでは、線幅が太くなり過ぎないように照射量を減らし、粗な部分では線幅が痩せないように照射量を増やす方法に取り組みました。 阿部さんが近接効果補正の研究に取り組み始めたのは東芝に入社した1984年以来のこと。1995年には直接描画において、電子ビームの照射時間と照射量を自動制御するための計算式を完成させ、コンピューター上のシミュレーションで精度が検証されていました。その研究成果を電子ビームマスク描画装置の開発にも適用しようとしました。 マスクの回路パターンは直接描画に比べて4倍に拡大されています。そのため、阿部さんは当初、直接描画に比べればマスクの近接効果はそれほど深刻なものとはならないだろうと考えていました。ところが、マスクを光で露光・転写する際にマスク上の誤差がシリコンウエハ上では誇張されてしまう現象が判明したのです。回路パターンの角の部分などが丸まったり、細くなったりする現象が現われ、それを補正するためにマスクの回路パターンには、直接描画以上に微細な加工を施す必要が出てきました(図6)。 この課題を解決するため、阿部さんは、マスク描画装置に特化した新たな近接効果補正技術の開発に挑戦することとなりました。過去10年間にわたる経験を活かし、試行錯誤の末、照射時間で制御される照射量を高速かつ高精度に算出する新たな計算式を完成させました。その結果、近接効果を補正しない時の寸法変動約200nmを2nm以下に抑えることが可能となりました。 図6 パターン寸法が露光波長より小さいと、光の干渉によってパターン像が歪み、これらを補正する微細で高精度のパターンをもつマスクが必要になった 図7 補正の効果 また、1995年当時は、たった数mm四方の照射量程度しか計算結果をメモリーに溜めておくことができませんでした。そこで、阿部さんはマスク上の一部の領域を描画している間に、その後に描画する他の一部の領域の補正計算が行えるように設計しました。加えて、電気回路で計算結果を高速かつ大量に処理できるように考えました。その結果、ほぼリアルタイムに照射量の補正を計算しながら素早く描画する装置を実現しました。 現在ではコンピューターの処理速度が非常に速くなり、並列処理も容易になったため、EBMの新型機ではコンピューター内でこれらの計算を行うようになりました。しかし、EBM-3000開発当時のコンピューター速度と容量ではこの実時間処理が現実的には不可能であったため、ハードウェアの専用電気回路を開発して実現したのです。 阿部さんと共同研究者は、この近接効果補正の発明、開発などにより、全国発明表彰第一表彰区分経済産業大臣発明賞(平成18年度、(社)発明協会主催)、科学技術分野の文部科学大臣表彰 科学技術賞(開発部門)(平成19年度、文部科学省主催)などの賞を受賞しました。 EBMの制御装置 FOR THE FUTURE 開発のいま、そして未来 新技術の研究開発継続で精度を向上 「可変成形ビーム」や、社内技術を進歩させた「リアルタイム近接効果補正」などを搭載して開発された電子ビームマスク描画装置「EBM-3000」は1998年に販売開始されました。順調に販売実績を伸ばすとともに、その後も同社ではNEDOプロジェクトにおいて研究開発を行い、その成果を装置改良へ反映させていきました。 2002年に発売された、「EBM-3000」の後継機「EBM-4000」には「フォギング効果補正」技術が開発・搭載されました。2005年に発売された「EBM-5000」では「低熱膨張描画チャンバー」が開発・搭載されました。 「フォギング効果」とは、マスクに照射された電子ビームが反射して、電子ビームを絞るための対物レンズに当たり、その散乱電子が再度フォトマスクに数センチにもわたる範囲で照射されてしまう現象です(図8)。 そこで、ハニカム型の反射電子防止板を作製し、対物ユニットの表面に設置しました。反射した電子が防止板の表面に斜めに開けられた穴の中に入り込むことで、マスクに戻るのを防ぐ仕組みです。従来に比べて反射電子の量を約4分の1に減らすことができました(図9)。また、この方法でも残る寸法変動を、場所に応じて照射量を変更することで補正する「フォギング効果補正」技術も開発し、更なる高精度化を実現しました。 図8 フォギング効果 図9 ハニカム型反射防止版の解説図(左)と顕微鏡による拡大写真(右) ナショナルプロジェクトだからこそできた挑戦 このような継続的な技術開発の成果が、競合機との性能差を大きくし、現在の世界シェア90%以上という結果につながっています。私たちの身の回りにあるデジタル情報通信機器のほぼ100%に、同社の技術が生かされているとも言えるほどです。また、同社の微細マスク加工技術があるからこそ、スマートフォンやタブレットなどの驚くべき小型・軽量化、高機能化が可能になったとも言えます。その上、これらの小型通信機器の普及の裏には、高速大容量のサーバコンピューターの整備増強も不可欠であり、これらのサーバコンピューターのほとんどもまた、同社の技術で製造されたLSIを搭載しているのです。 服部さんはプロジェクトを振り返ってこう話します。「電子ビームマスク描画装置の開発の始まりは社内使用でした。売り上げ実績のない機器の開発に挑戦できたのはやはりNEDOの支援があったからこそ。ナショナルプロジェクトだからこそ挑戦できたと同時に、だからこそ商用化を実現しなければという、良い意味でのプレッシャーを感じながら研究開発を行えました」 また、阿部さんは、「それまでの社内向け装置の開発ではなく、ナショナルプロジェクトということもあり、チームメンバーが一丸となって商用化に向けて頑張ることができました。高加速電圧電子ビームマスク描画装置の技術は成功すれば、必ず息の長い技術になるだろうと予測していましたが、予測通りプロジェクトで開発した各種要素技術は今でも次世代の装置開発の礎となっています。また、EBMシリーズは、弊社の売り上げにも大きく貢献してくれています」とも話します。 新技術の寿命が短い半導体関連機器の中にあって、同社の微細マスク加工技術は10年以上にわたって世界最先端を維持し続けています。現在も次世代機の研究開発が進行中であり、今後も同社の電子ビームマスク描画装置は、情報通信機器の発展を支えていくことでしょう。(2012年11月取材) EBM本体の外観 開発者の横顔 社内初の商用化を目指しチームが一丸となった マスク描画装置の開発はパズルを解くようなもの 吉川良一さんは1978年の東芝入社以来、マスク描画装置開発一筋の技術者です。2009年まで、ニューフレアテクノロジーの常務取締役であり、現在は顧問を務めています。 「マスク描画装置の開発では主に電子ビームの制御系を担当しました。マスク描画装置の開発はパズルを解くようなもので、一つ解けると他も一気に解けたりして、とても面白かったです。とは言え、プロジェクト自体はマラソンと同じで、地味で大変な作業の連続でした。それだけにゴールに到達した時は大きな達成感がありましたね」 株式会社ニューフレアテクノロジー吉川さん 初の商用化ということでプレッシャーの連続だった 大学院時代は保健学を専攻し、保健学博士を持つ服部芳明さん。大学院修了後は東芝の系列会社である日本原子力事業で保健学の知識を活かし、ヒューマンエラーに関する研究を基に原子力発電所の運転支援システムの開発を行っていました。1989年に同社が東芝に吸収合併され、1996年に東芝機械に出向、以来、マスク描画装置の研究開発に携わっています。 「NEDOプロジェクトでは、成果をきちんと出さないといけないので、緊張の毎日でした。特に、当社初の商用化ということでプレッシャーも大きかったです。しかしながら、努力の甲斐あって、今や世界一のシェアを実現することができ、大変満足しています」 株式会社ニューフレアテクノロジー服部さん 初号機の商用化を皮切りに次世代の商用化を波に乗せることができた 1982年に東芝に入社した玉虫秀一さん。元々の専門分野はシンクロトロン放射です。そのため、電子ビームマスク描画装置の開発では、主に偏向器の設計、偏向器の自動制御を担当しました。 「NEDOプロジェクトで電子ビームマスク描画装置を商用化すると聞いた時には、本当にできるのかなと思いました。というのも、これまで描画装置は数年で1台というペースで開発、製造していたからです。それが、年間数台も製造できるのかなと思ったのです。でも、初号機の商用化を皮切りに、その後も順調に商用化できて良かったです。最初は単なるスイッチの入れ忘れなどちょっとしたミスなどが原因で、わけの分からない現象が起こり悪戦苦闘しましたが、今は良き思い出です」 株式会社ニューフレアテクノロジー玉虫さん 私が考えた計算式を基に実際にフォトマスクが作製されたときは感激 大学院時代は理論物理の中でも物理学と数学の境界領域に当たる統計力学を研究していた阿部隆幸さん。1984年に入社以来ずっと近接効果補正に関する研究を行ってきました。そして、電子ビームの照射時間と照射量をコンピューターによって自動制御するための計算式を完成させたのです。 「計算式は完成しても、それを実際にシステムとして実現するとなると話は別です。いくら高精度で設計通りに回路パターンを再現できたとしても、計算に膨大な時間がかかってしまっては、実用化は困難だからです。そのため、いかに計算量を減らし実時間内で計算を終わらせながら、高精度を維持するかも大きな課題でした。また、大学院時代は理論中心でしたので、私が考えた計算式を基に実際にフォトマスクが作製されたときには感激し、大きな手応えを感じました」 株式会社ニューフレアテクノロジー阿部さん なるほど基礎知識 半導体集積回路(LSI)の製造プロセスとフォトマスク LSIとは抵抗、コンデンサ、ダイオード、トランジスタなどの電子部品が多数、シリコンなどの半導体基板上に集積した電子回路のことです。 そのため、LSIの製造は回路設計から始まります。回路設計が終わったら、フォトマスクの原画となるマスクパターンを設計します。 次に、マスクパターン設計を基にフォトマスクを作成します。フォトマスクは、LSI製造の露光工程で使用する転写用の原版です。シリコンウエハの上に電子回路を転写するために使います。写真にたとえれば、フォトマスクが写真のネガフィルム、シリコンウエハが印画紙に焼き付けられた写真ということになるでしょう。 シリコンウエハ上に電子回路を作る工程はリソグラフィ(フォトエッチング)技術を用いて行われます。数十枚の工程別に分解されたフォトマスクの原版に描かれた回路パターンを、何度もリソグラフィ工程と成膜工程を繰り返しながらシリコンウエハに転写することで、素子を形成していきます。最後に素子に電極を形成します。 1枚のシリコンウエハには同じ回路パターンを持つ複数の素子が作製されます。それら一つ一つ切り出し、回路基板に固定し、電極接続をするなどの組み立て工程を経て検査に合格すれば、LSIの完成です。 図10 半導体集積回路の製造プロセス NEDOの役割 「超先端電子技術開発促進事業」 このプロジェクトがはじまったのは? プロジェクト開始当時、高度情報社会を支えていくため情報通信機器の高性能化が求められ、そのためには半導体集積回路(LSI)のさらなる微細化が不可欠でした。また、わが国の国際競争力を維持するためには、半導体デバイスの製造プロセスにおける先端技術の確立が必要と考えられました。NEDOでも、1995~2001年にわたり、「超先端電子技術開発促進事業」プロジェクトを実施し、半導体製造プロセスの中でもコア技術と言える「リソグラフィ技術」の高度化を支援しました。 プロジェクトのねらいは? 半導体の微細化や高集積化の根本となるのが、回路をシリコンウエハに形成するリソグラフィ技術です。リソグラフィ技術は様々な技術要素からなる総合システム技術で、プロジェクト開始当時は電子ビームリソグラフィに次世代技術としての注目が集まっていました。従来の光リソグラフィ技術が限界を迎えることも予測され、次世代リソグラフィ技術の確立は緊急課題になっていました。本プロジェクトでは、そうしたリソグラフィ技術の中でも、半導体集積回路の微細加工技術の中核となるマスク作成技術の高精度化、生産性の向上を目標に、高速・高精度のマスクパターン作成技術確立を目指していました。 NEDOの役割は? 半導体集積回路の微細化、高集積化の進行に合わせて、マスク作成の高精細化を果たすためには、解決すべき技術的困難性が高いこと、また、先端的技術の研究開発のため、技術的、経済的リスクが大きいことから、NEDOプロジェクトとして支援することとなりました。とくに、プロジェクト開始当時は米国企業のシェアが高く、わが国の民間企業にも技術的な蓄積はあったものの、マスク描画装置の市場規模が小さいため、開発費負担と事業規模が見合わず、次世代描画装置の開発が進まない状況にありました。本プロジェクトにより、わが国のマスク作成技術は飛躍的に向上し、1997年当時35%程度だった日本製の電子ビームマスク描画装置のシェアを90%以上まで高めることに成功しました。 関連プロジェクト 「超先端電子技術開発推進事業」プロジェクト(1995-2001年) お読みいただきありがとうございました。ぜひともアンケートにお答えいただき、お読みいただいた感想をお聞かせください。いただいた感想は、今後の連載の参考とさせていただきます。 アンケートに回答する (法人番号 2020005008480) NEDO WebMagazineとは サイト利用について ©New Energy and Industrial Technology Development Organization. All rights reserved. Top -->
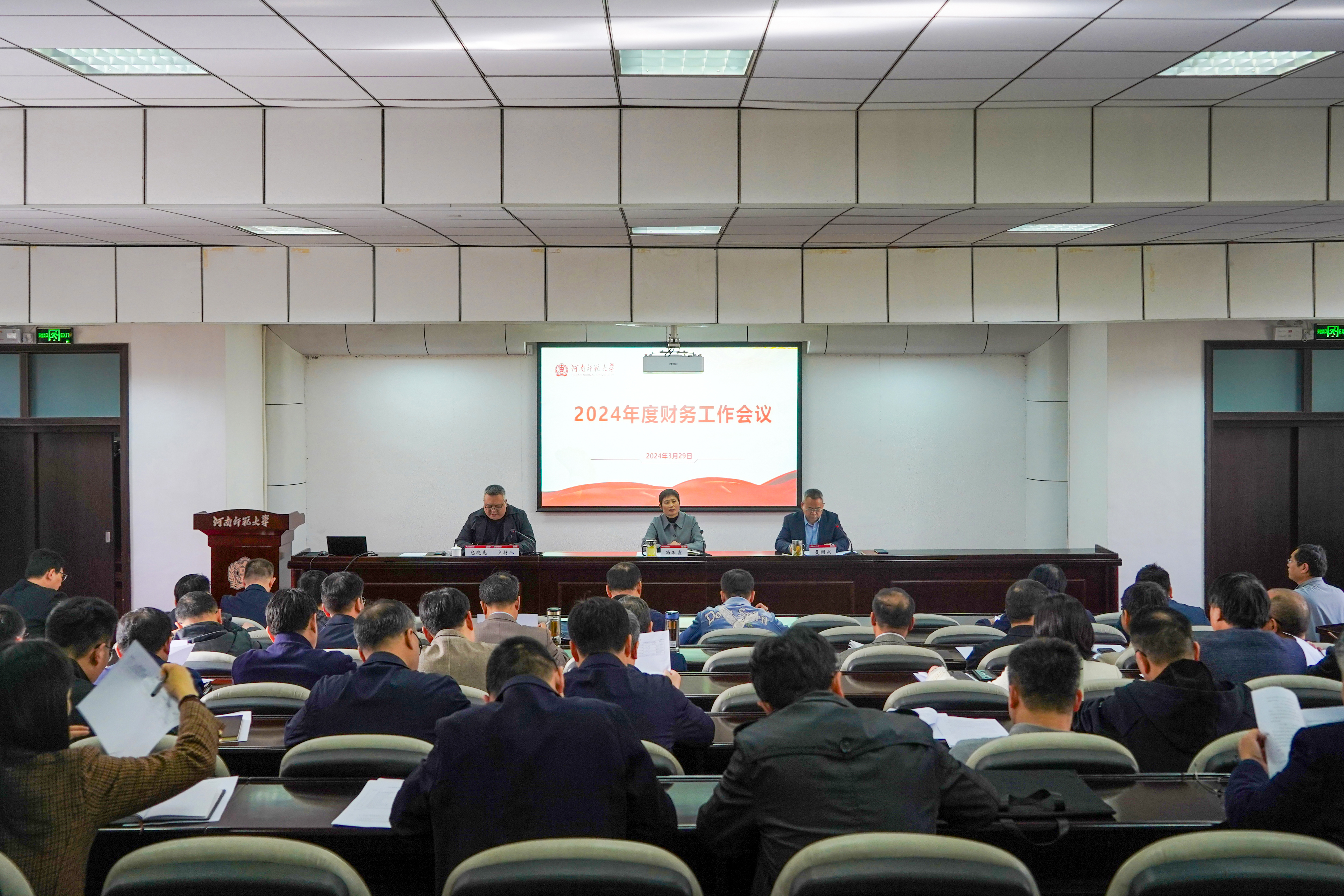